When wood burns, what’s really going on?As I understand it, it’s a 2.5 step process.
1) Heating the wood causes it to vaporize into its component molecules.
1.5) depending on the temperature, the longer, more complex molecules decompose into simpler molecules. Larger molecules don’t burn as well. Axle grease doesn’t really burn. Gasoline does. If you heat up axle grease enough, it will break down to something that will burn.
2) The simpler molecules burn and the larger ones got up in smoke.
The point of my rocket stove is that the fire happens in a hot space and I get more complete combustion due to that concentration. That’s been working pretty well.
Over the last year or two, I’ve read a couple times about
Terra Preta and how it can be used to help revitalize farming soil and also serve as carbon sequestration. After I hear about it again on
Science Friday. In the story, the guest described the charcoal making process as simply heating wood to about 400 or 450 degress F in an oxygen poor environment. This was also something that I’d read and thought about before due to
this site
So I figured, why not try it myself? My results have been good so far, but the process makes too much smoke.
First, I took some left over ducting and, together with two end caps, I make a canister about 10″ diameter and 16″ long. I suspended this canister inside a piece of 12″ diameter ducting. I suspended them with screws similar to how I did the rocket stove.
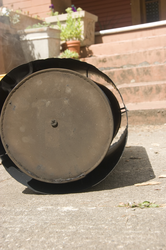
I then crimped the end of the 12″ ducting so I would fit snugly on the stove.
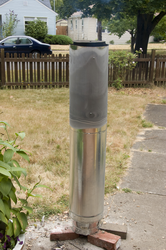
On the first try, I put a vent hole on the top, but this was not such a good idea because it produced a LOT of smoke. I removed it from the stove and let it cool off. I sealed the hole with a bolt and drilled a hole on the bottom. This worked better, but still had more smoke than I cared for.
Since smoke means incomplete combustion, I need to channel the smoke into the heart of the fire, so I took a piece of iron pipe I had around and had it extend from the bottom of the canister down into the fire.
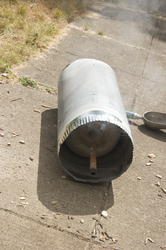
This helped things a bit, but the canister itself wasn’t sealed all the well. Smoke was escaping through the seams. Not realy sure how to fix that. The whole thing heats up enough that solder will melt. to attach the iron pipe, I used a ring bolt from my box of electrical parts. It’s from one of those things that hold wires onto a metal junction box. Anyway, it melted off!
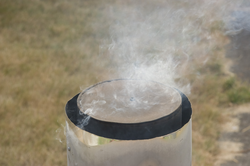
so the experiment hasn’t quite panned out. If I were living in the country, it’d be good enough, but here in the city,… not so much.
Here’s the first batch. Charcoal. If you take a piece of it and break it, it’s consistent throughout.
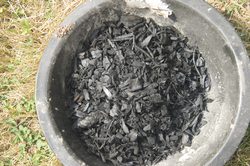
So the next step will be to figure out a way to seal the canister or to make another one that doesn’t have these issues. Maybe #10 food cans. I’ve also thought about some sort of shroud to expose the smoke to more heat. will hvae to think about it some more.
Here are some more cool fire pictures. 😉 Oh. One thing I forgot to mention. I added more holes inside the rocket stove, so there more airflow. It doesn’t burn like this for very long, but it’s pretty spectacular.